Equipment for complex oil
treatment
Integrated hydrocarbon treatment scheme
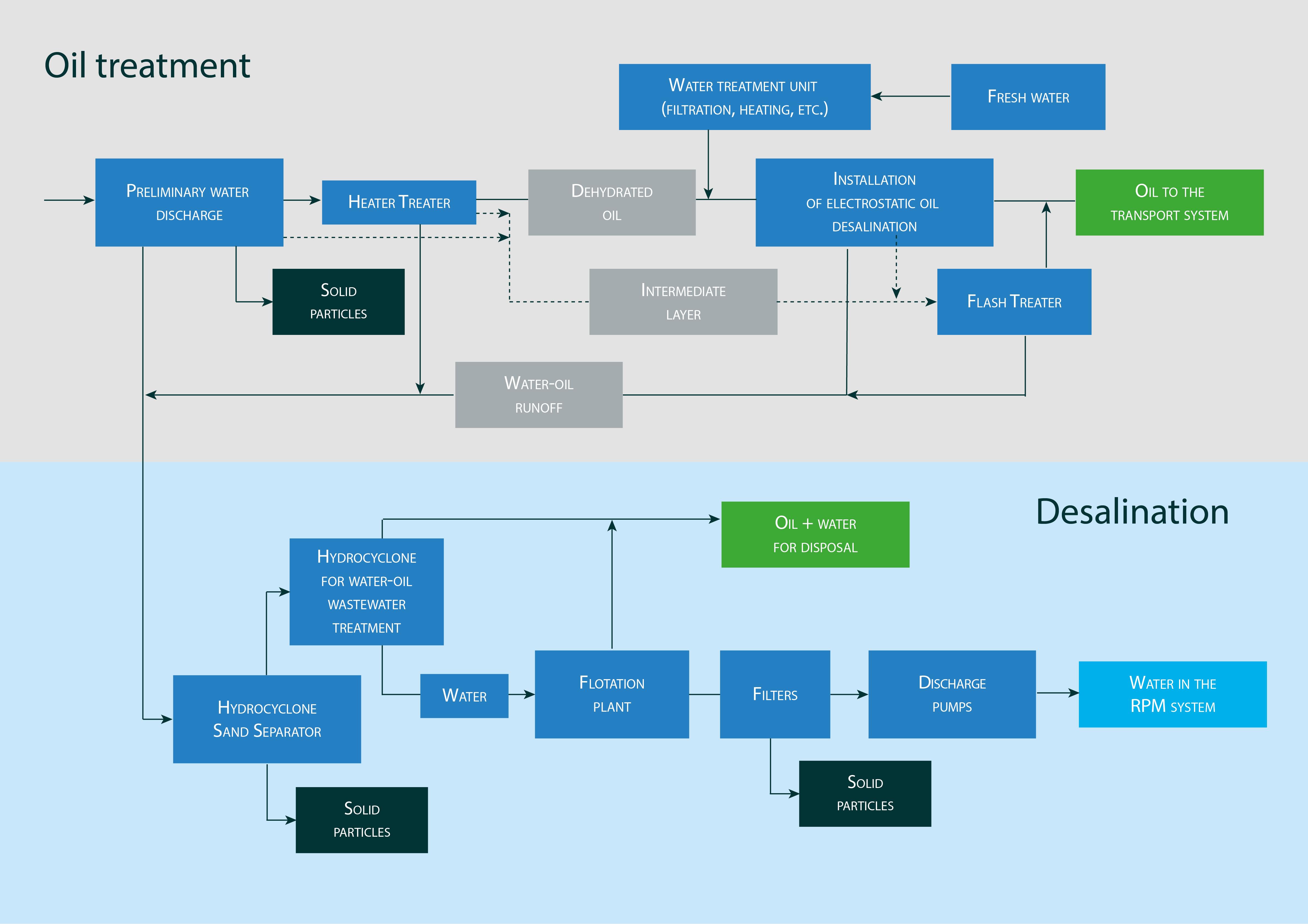
Oil treatment plants before transportation
Oil pumped out of wells comes to the surface together with formation water, associated gas and rock solid particles. Primary treatment consists in separating the mixture into components. Gas separation is relatively easy; however, oil together with water form an emulsion.
Since the presence of water in oil significantly increases transportation costs, it undergoes mandatory dehydration.
Oil dehydration and desalination plants
To remove liquid and mineral salts from crude oil, the following equipment is used:
- Heater-Treater and preliminary water removal unit (PWRU).
- Gravity separator;
This equipment provides direct oil heating and gravity separation.
Oil treatment unit (Heater-Treater)
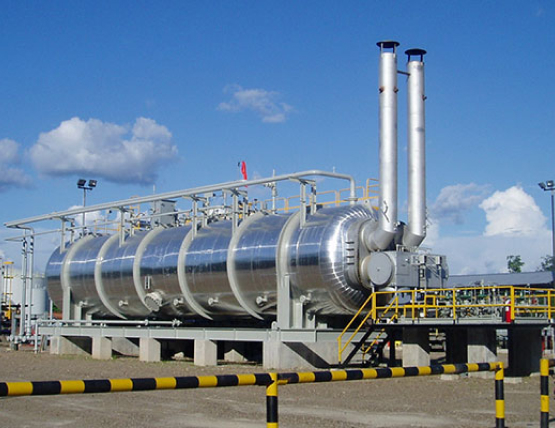
Thanks to its versatile functionality, one Heater-Treater unit is capable of replacing several cleaning systems at the same time.
Heater-Treater is an oil and gas water distributor with direct heating, which can perform several functions at once, while other oil purification systems perform them only separately. These are:
- Dehydration of crude oil
- Its separation into oil and by-products
- Obtaining refined oil from primary raw materials
The oil and gas water distributor can operate even in the harshest climatic conditions: the device withstands air temperatures down to -60 °C. Despite the fact that the equipment is installed in an open area, it is resistant even to the strongest wind gusts. The set is initially delivered ready for operation, which saves on installation costs.
Principle of operation of the Heater-Treater
The feeding of crude oil into the Heater-Treater is carried out through the inlet choke located in the upper part of the tank. Separation of liquid and gas takes place in the inlet compartment. As a result of the separation process, gaseous substances are removed from the apparatus through the outlet.
In the moisture extractor, all the liquid in the gas is coagulated and combined with the liquid phase at the bottom of the tank. Meanwhile, the gas enters the regulator valve, which is responsible for the pressure and oil level in the system.
A constant temperature in the furnace and flame tubes of the Heater-Treater system is maintained due to the processing of associated petroleum gas entering the apparatus from the oil preparation unit. The temperature level is maintained by special regulators and control devices with which the control unit is equipped.
Advantages of the device
- Multifunctionality: The unit can perform several oil refining functions at once;
- Unlimited separation of primary raw materials, regardless of pressure;
- Low water concentration (less than 5%) due to modernized filtration systems;
- Increased fire safety;
- Automatic security control system.
Gravity Oil Separator (Oil & Gas Separator)
The operating principle of separation units is based on the division of the substance flow due to gravity. Oil and gas separators are used for degassing the oil mixture as well as purifying the associated gas. In the separation process, the gas moving through the pipes at low velocity allows water and other substances, particularly solid impurities, to settle to the bottom of the vessels. Meanwhile, the purified oil flows to the outlet pipes.
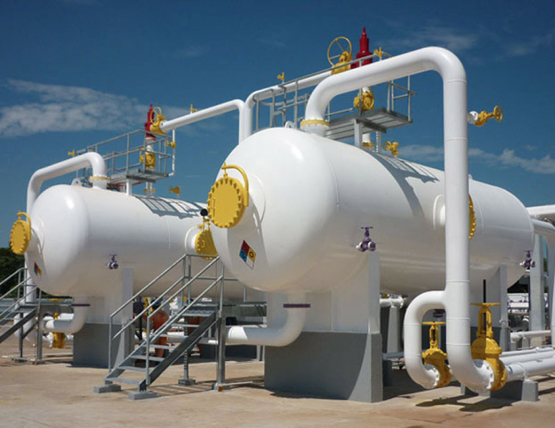
Classification and specific features of use
According to their design features oil separation devices can be horizontal or vertical. Both devices have their own distinctive advantages:
- Horizontal models are chosen for their highest performance;
- Vertical models are installed in engineering systems with limited area, for example, on production platforms or floating devices.
Depending on the purpose, gravity separators are divided into:
- Three-phase gravity separators: separate the oil mass into oil, associated gas and formation water;
- Gas-liquid (gas) gravity separators: purify natural and associated gases from various mechanical impurities, water, condensate and other liquids;
- Measuring gravity separators: to determine the amount (volume) of oil that has been refined through the separation tank, as well as the amount of by-products (associated gas and formation water);
- Scrubbers: for cleaning gas from various solid particles by exposing it to a liquid (by spraying a gaseous mass with water).
The only disadvantage of the gravity separation system is the large overall dimensions of the installation. After all, the diameter of the gravity separation is much larger in comparison with the diameter of the gas pipeline.
Equipment for oil treatment at refineries
It is known that extracted oil raw materials contain a certain share of water and solid particles, in particular mineral salts. The presence of salt in crude oil not only negatively affects mechanisms (which use petroleum products), but also hinders various physical and chemical reactions, so before the oil raw material is sent for processing, it must be cleaned of liquid and other impurities.
Since the salt in oil is dissolved in water, electric dehydrators (ED) are usually used in refineries for a set of works on dehydration and desalting of crude oil.
The operating principle of electric dehydrators is as follows: an alternating current generates an electrostatic field through which the oil emulsion passes, releasing the residual moisture.
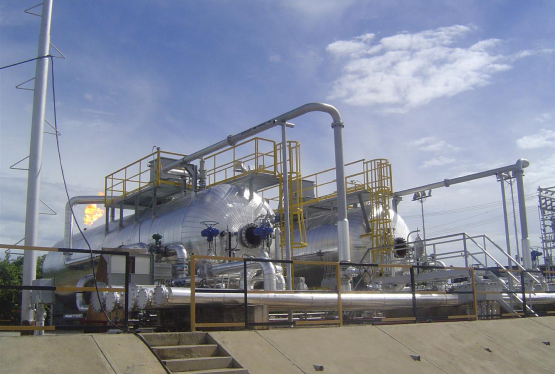
Classification and features of electric dehydrators
By design features, there may be following types of electric dehydrators:
- Ball electric dehydrator. The device can accumulate an unlimited amount of processed raw materials. However, it cannot be used at elevated temperature and maximum pressure.
- Horizontal electric dehydrators. The most efficient cylindrical units. They are distinguished by the ability to work even at elevated pressure and high temperatures.
- Vertical electric dehydrators, which are similar in tank shape to the horizontal ones. However, in contrast to them (and ball ones) are used quite rarely, which is due to their low capacity, as well as the possibility of using the systems only at relatively low pressure and minimum temperature.